Root cause: There’s probably no such thing
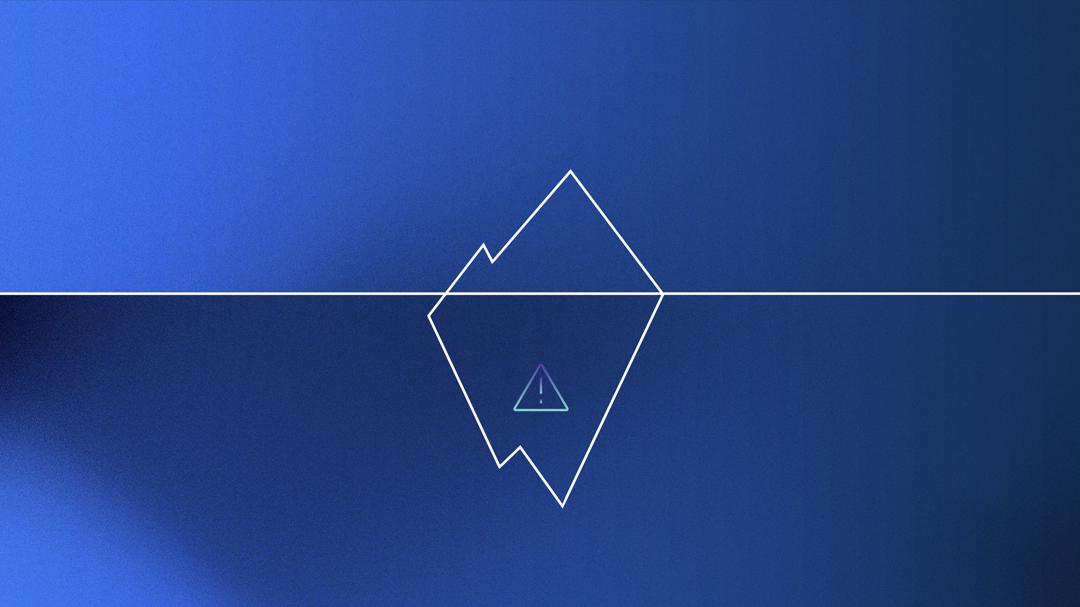
When things go wrong in the workplace, we often feel compelled to identify one factor that could have prevented the incident. This desire stems from a cognitive bias and a need to impose order on the chaos that follows such events.
This reflex leads us to oversimplify complicated situations, as we search for a clear answer amid doubt. However, this approach can overlook the complex web of factors that contribute to incidents, ultimately hindering our ability to learn and improve risk prevention.
What’s the solution? A SCALE® analysis. Discover the benefits these have for large organisations and how, when properly implemented, they can prevent serious incidents.
The reality of incident investigations
As an example, in 2024, we reviewed 30 serious incident investigations for one of our clients. These incidents could have resulted in a worker's death, if they hadn’t been lucky.
Among these investigations, two few stood out as insightful analysis. By that we mean, they were thorough and unbiased explorations of complex challenges in today’s workplaces. Many issues were considered and uncovered in these detailed investigations.
Sadly however, the other 28 investigations were not that standard. Let’s look at how the majority of serious investigations lead to repeat incidents.
The appeal of structured processes
It’s tempting to believe a well-branded investigation process will lead to reliability. But how many organisations have successfully stopped repeat failures using this approach?
Having neatly structured processes won’t guarantee improvement. It requires intent, curiosity, and a commitment from all parties involved to treat failures as opportunities for learning and growth.
The solution: Embrace causal analysis nor root cause analysis
Instead of searching for a single root cause, organisations should adopt a more comprehensive approach to root cause analysis (RCA); an analysis that considers multiple causes. This method involves:
- Defining the problem: Clearly articulate what went wrong and where it occurred. If safe to do so, begin collecting information immediately after the incident occurred.
- Collecting data: Gather the relevant information about the incident. If you need help with this, our diagnostic and advisory services may have your solution.
- Identifying possible causes: Consider all factors that may have contributed. These could be equipment failure, environmental events, or human error. Remember to speak with all parties involved and review security footage – if possible.
- Determining the causal factors: Use techniques like the SCALE® to drill down into underlying issues.
- Implementing corrective actions: Develop what you need to do to address identified root causes of the issue.
- Monitoring and reviewing: Make sure your corrective actions are effective and adjust them when needed. Reviewing these processes bi-monthly, quarterly, or annually can help address issues before they become problems.
What’s next for your organisation?
By following these steps, organisations like yours can enhance your incident risk management processes and nurture a culture that prioritises preventing serious incidents – not merely focusing on assigning blame.
Our Incident Investigation Course can help you improve your organisation’s approach to serious incident investigations. This training will equip your team with the skills needed for more effective causal analysis and help prevent serious incidents and fatalities in your workplace.
For more resources on enhancing incident prevention and risk management, explore our diagnostic and advisory services .
Get in touch
Let us show you what we can do for your business