Why Aren’t Organisations Learning from What Goes Wrong in Their Operations?
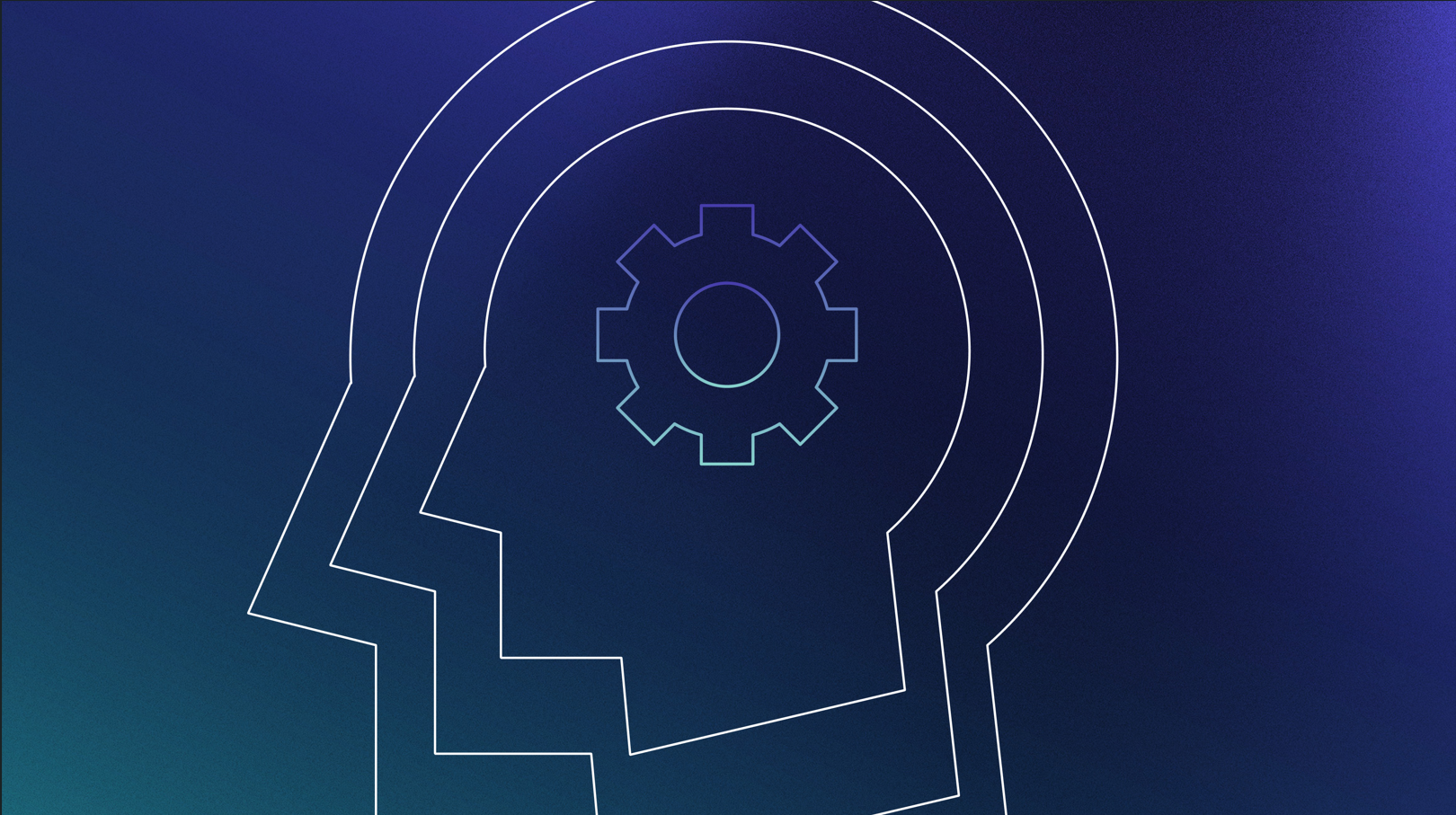
It’s a familiar story: an organisation experiences a serious incident, launches a detailed investigation, and produces an exhaustive report packed with recommendations. Yet, months later, the same issues resurface, leaving the organisation back at square one. Why does this cycle persist?
Too often, the blame falls on human error, with superficial remediation efforts aimed at changing behaviour. The result? Repeat incidents, frustrated leadership, disillusioned frontline workers, and an unchanged risk profile.
But there is a way forward. By shifting the focus from blame to learning, organisations can break free from this cycle and create lasting change. Here’s how:

The Learning Challenge
Reducing exposure to serious incidents is not just a matter of identifying errors—it’s an organisational learning challenge. True learning requires objective investigation, free from biases that can cloud judgment.
At its core, learning from failure isn’t just about analysing what went wrong but also about understanding how work is being done. This includes examining critical controls and how they’re applied in practice.
Over years of working with organisations, we’ve developed a proven, repeatable process to turn incidents into opportunities for operational reliability. Here's our approach:
- Assess the incident’s severity: Determine whether it’s worth investing resources into a full investigation. Not all events require the same level of scrutiny.
- Identify ineffective or absent critical control: Pinpoint which safeguards should have protected workers but didn’t.
- Analyse contributing factors: Investigate whether breakdowns were influenced by human, site, or organisational factors—or a combination.
- Implement meaningful changes: Develop recommendations that address the contributory factors causes and significantly reduce the likelihood of recurrence.
By following these steps, organisations can dramatically reduce their exposure to risk and foster a culture of continuous improvement.

Why Focusing on Human Error Is Important but Not Enough
Blaming human error often oversimplifies the problem, missing the opportunity to address deeper systemic issues. Let’s explore some common challenges tied to human performance and how they can be mitigated:
1. Employees on Auto-Pilot
Repetitive tasks can lead to workers zoning out, making it harder to detect changes or emerging risks. Regular check-ins and supervision can provide “mental nudges” to help workers stay alert and engaged.
2. Cognitive Fatigue
Cognitive fatigue can be more dangerous than physical exhaustion, impairing judgment and reaction times. Address this with a validated fatigue risk management system. Ensure workers have sufficient breaks and rest periods, tailored to your industry’s specific needs.
3. Memory Failure
Complex tasks that involve more than four or five steps can exceed a worker’s memory capacity, leading to errors. Simplify processes where possible or implement step-by-step cross-checks.
4. Group-Think
Team dynamics can discourage workers from speaking up about risks. This is particularly common in hierarchical environments. Pre-start meetings should encourage open dialogue, and leaders should create avenues for workers to voice concerns confidentially if needed.

Spearheading Change
High-quality learning should always be the first priority for organisations aiming to prevent repeat incidents. To achieve this, invest in the skills and tools your team needs to analyse incidents effectively and implement meaningful change.
We offer a comprehensive SCALE Incident Investigation Course that equips teams with the expertise to conduct in-depth accident causation analysis. By focusing on root causes and systemic factors, your organisation can move beyond surface-level fixes and build a safer, more resilient workplace.
It’s time to stop blaming and start learning. With the right approach, your organisation can break the cycle of repeated incidents and foster a culture of safety and continuous improvement.

Want to learn more about improving your organisation’s learning practices? Contact us today to find out how we can help you reduce risks and prevent serious injuries and fatalities. Sign up to our Incident Investigation e-Learning course to find out more about effective tools to help prevent serious incidents.
Get in touch
Let us show you what we can do for your business